Remove flywheel and clutch disc.
If you also need to remove the clutch pressure plate, use a screwdriver to remove the locking ring of the switching off plate.
Loosen the 6 screws in the pressure plate.
Remove pressure plate with disc spring.
Blow out the flywheel with compressed air or wipe it with a rag soaked in gasoline. Take this opportunity to check whether the centering pins are firmly fixed in the flywheel.
The old pressure plate can only be installed if the riveted joints are still sufficiently secure.
The surface on which the drive disc rests must be free of cracks or burnt spots. Deflection - no more than 0.33 mm inside. To measure, place a metal ruler across the pressure plate and use a feeler gauge to measure at the inner edge.
Insert the disc spring into the pressure plate.
Lubricate new bolts with preservative. The tightening torque must be 75 Nm.
Apply a small amount of grease to the thrust disc bearing surface and surface. with which the clutch pusher is in contact.
Insert the separating disc in this way. so that its groove for the clutch pusher is directed towards the gearbox.
In the clutch assembly with a drive disc having a diameter of 190 mm, the ends of the fixing ring must be directed towards the gearbox. If the disc diameter is greater than 200 mm, the ends must point towards the motor.
Lubricate the internal splines of the drive plate with a small amount of grease so that the drive slides well on the gearbox shaft.
Insert the clutch drive plate, the protruding spline must point towards the gearbox.
Install the flywheel so that its centering pins fall into the corresponding holes or slots in the pressure plate. Otherwise there will be no mark match "FROM" on the flywheel and pressure plate.
When tightening the flywheel bolts, the clutch drive disc must be centered. For this, workshops use the special tool 547.
Auxiliary technique: you can, without tightening the flywheel mount, check the gap between the outer edge of the drive disk and the inside of the flywheel. This will require a sliding caliber.
The gap must be the same size around the entire circumference. Otherwise, shift the clutch drive until it is exactly in the middle. Tighten the flywheel screws with a torque of 20 Nm.
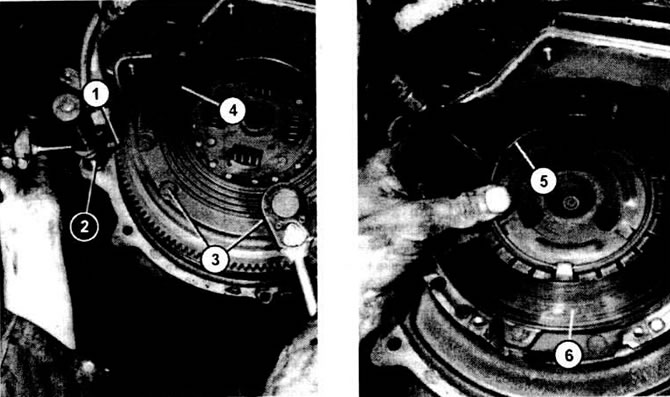
The illustrations show the dismantling of the clutch. Left: for loosening screws (3) flywheel (4) insert screwdriver (2) into one of the holes, and the second screwdriver (1) - into the ring gear and fix with this screwdriver. Right fixing ring (5) pressure plate (6) barely raised.
Visitor comments