2. Using a valve spring compressor, compress each spring in turn so that the cone guards can be removed (locks). After removing the conical safety rings, release and remove the valve springs together with the poppets. If it is difficult to remove the fuses, do not bend the springs further, but pry them with a screwdriver. It is best to use tweezers to remove the fuses.
3. Before removing the valves from the head, it is necessary to note to which cylinder it belongs. To do this you need:
- fill on the valves of the first cylinder - one point at a time,
- the second - two points,
- third - three points,
- fourth - do not fill points
The points are filled with a center punch (on intake and exhaust valves) from the side of the combustion chamber, when the valve is securely supported by the entire perimeter of the key on the valve seat. We can fill such points on the surface of the combustion chamber so that there is no doubt during installation. The first cylinder is located near the timing belt, the fourth cylinder is near the flywheel.
After the valves have been removed, they must be inspected. Very deep scratches on the sealing surface that cannot be grouted qualify the valve as requiring replacement. We do the same when the valve is bent or burned out. The end of the rod must be ground to eliminate traces of the action of the valve lever or pusher. Carbon can be removed from the stem with a rotating metal brush.
4. Check the condition of the valve levers. If a certain wear is noticeable on the contact surface of the lever with the cam, then the lever is replaced with a new one. If a dent is noticeable on the operating surface of the lever and valve stem, then the surface of the lever must be sanded.
5. Then we check the condition of the valve springs. Broken springs, damaged or after a long run must be replaced with new ones. If there is any doubt about their condition, the bending of the spring can be checked at a specialized company under a certain pressure.
6. Remove the valve guide seals. Then remove the lower valve spring seats (photo 1.116).
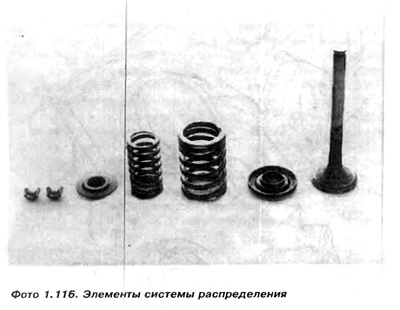
7. No need to unscrew the ball head bolts (pic. 1.5), except that this will only be necessary if they are damaged, since there is a possibility of stripping the threads in the head.
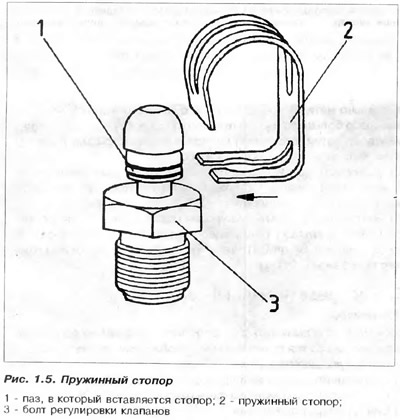
8. Carbon deposits must be carefully removed with a scraper so as not to damage the sealed surface of the head and valve seats.
It is also necessary to clean the valve disc, paying attention to its sealed surface. A common engine fault caused by a lot of soot is self-ignition or difficulty in adjusting the correct ignition timing. This is detected when fuel is burned with a knock in the engine, if the ignition timing is set according to the adjustment data.

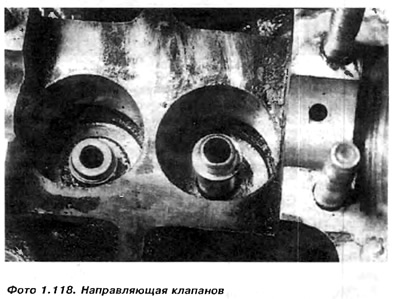
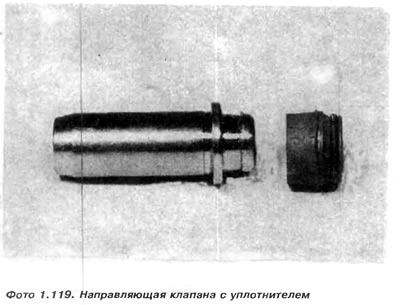
9. Using a scraper, it is necessary to remove all the remnants of the gaskets, then rinse the head with kerosene, rinse with water and blow with compressed air.
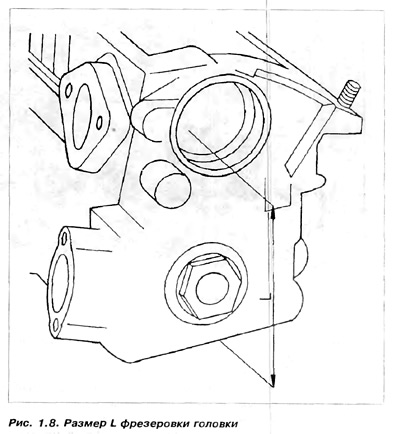
10. Check valve guide bores for wear and replace if necessary. We check the wear of the guide by inserting a new valve into the guide and measuring the advancement of the valve disc perpendicular to the valve axis, from one extreme position to another. The valve must be inserted so that the top of the valve stem is in the same plane as the top of the valve guide. The amount of this movement should not exceed 1 mm for the inlet valve and 1.3 mm for the exhaust valve. For an old valve, these values may be slightly higher. It is necessary to check the guides one by one. if the measured values (when using a new valve) more data, then the guides need to be replaced. We knock out the used guide with a hammer through a mallet centered on the hole, or squeeze it out with a press (photo 1.120). The new guide must be pressable and it is recommended to heat the head up to 70°C. We can also put the guide in the freezer. Before knocking out the old guide. it is necessary to measure it, how much it rises above the surface with the head, and also press in a new one. Before pressing in, the hole in the head and the guide must be lubricated with oil. Install the head on the press riser so that the axis of the hole in the head coincides with the axis of the press piston. After pushing in, check the data above the amount of valve travel.
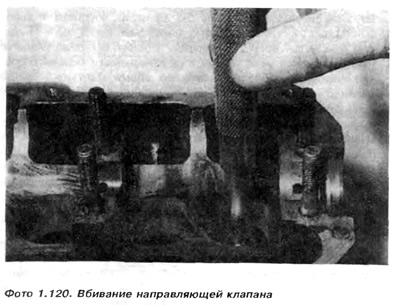
If a micrometer and bore gauge are available for small bores, the measured mounting gap between valve and guide should be between 0.03...0.06 mm for new parts and up to 0.15 mm for used parts.
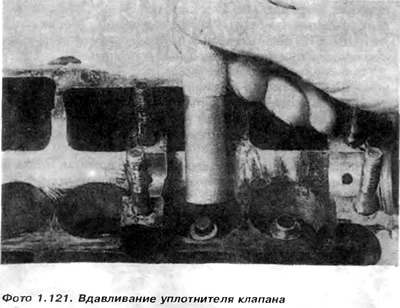
If the internal hole of the corrector undergoes deformation during indentation, it must be drilled out with a calibration drill.
The interference between the new guide and the hole in the head should be between 0.06 and 0.10 mm.
11. Using a ruler and a gap gauge, it is necessary to check whether the surface of the head has undergone deformation. Pay special attention to the surface between the combustion chambers. The sunken surface in these places entails a weaker gasket pressure. Since the distance between the cylinders is not very large, loose gasket pressure increases the possibility of gasket burnout. If at any place between the ruler and the head it is possible to insert a gap gauge with a thickness of 0.1 mm, then it is necessary to carry out the surface treatment of the head at a suitably equipped mechanical plant. A common reason for the curvature of si heads is uneven clamping or pressing without loosening all the bolts, and later - their complete unscrewing. The size L is indicated in the technical data. If the layers removed during machining are larger than 0.5 mm, milling of the valve seats is necessary to lower the valves deeper by the thickness of the layer removed. This is necessary to prevent the piston from hitting the valve and avoid valve distortion. This operation is carried out with cutters for valve seats, which are centered along the axis of the valve guide. The seat must also be milled when there are traces of corrosion and burnt spots are visible, as well as when the pilot valves have been replaced. If the corrosion is small, it is enough to remove it with a grinding paste.
Caution: The valve seats must be replaced by a specialist company, as certain conditions must be met during installation.
Before pressing the socket head, it is necessary to heat up to 320°C or cool the nest in liquid nitrogen and heat the head to 100°C.
12. Ways to repair valve seats: valve seats are repaired by milling and grouting or grinding and grouting. Let's discuss the first method, because. grinding requires a very expensive grinding machine. Hand grinders do not guarantee adequate machining accuracy because they transmit vibration from the electric motor (in our grinding machines are often unadjusted). They are effectively used to remove the hardened surface of the valve seat. After grinding on a stationary grinding machine, grouting is not needed. Milling has the disadvantage that grouting is necessary, because the surface of the socket after processing is slightly wavy. We insert a cutter with an angle of 90°into a chuck with a centering rod, which we insert into the hole of the directional valve and. pressing it to the socket, slowly rotate it clockwise. The condition for proper processing is:
A) Making a fitting surface in the form of a flat strip with a width of 1.5 to 2.0 mm (pic. 1.8)
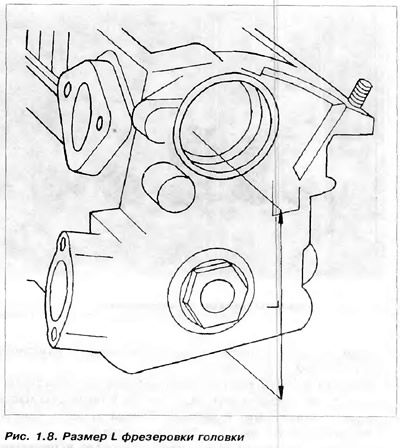
b) The angle of inclination of this strip should be 90°, and the surface of the strip should be axial with the opening of the valve guide.
If during milling the width of the strip exceeds the permissible limit, it is necessary to reduce it using two additional cutters with first 150°and then 30°angles, with a cutter with an angle of 90°. The main problem is maintaining alignment Often the valve guide bores and centering rod have a gap that prevents misalignment.
A misaligned socket will require long grouting. You can try to avoid this. After milling the socket (before grouting) it is necessary to insert the corresponding valve, press it lightly with your finger to fit, and with the other hand turn it several times so that it fits normally into the socket. Insert a hose with compressed air into the inlet or outlet manifold, only not under very high pressure. Then a little kerosene must be poured onto the pressed valve. Air bubbles that appear will indicate places where the valve does not fit into the seat. It is the lack of coaxiality that has such an effect that the valve disc only partially fits along the perimeter with the seat. With a certain skill and several attempts, you can correct the alignment error.
Visitor comments