Input shaft
The input shaft does not need to be adjusted. It is important, however, that the washer found during dismantling. was re-inserted during assembly.
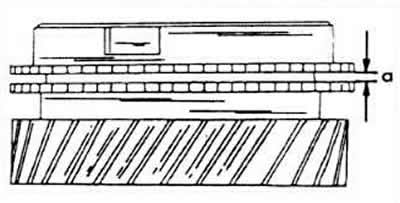
Before assembling the shaft, place the 3rd and 4th gear synchronizing ring on the appropriate pinion cone and use a feeler gauge to measure the gap between the gear and the ring. The wear limit is 0.5 mm, while the initial value for the third gear synchronizing ring is 1.15-1.75, and for the fourth gear ring is 1.3-1.9 mm. The same value for the fifth gear synchro ring.
If it is necessary to replace the bushing and oil sealing ring at the end of the shaft, knock out the parts from the inside using a ten mm round rod. Fully drive in the new bushing. From the outside, the sealing ring is equipped with a plug. Drive in the item until then. until the plug rests against the collar, then remove the plug. Lubricate the lip of the sealing ring with oil.
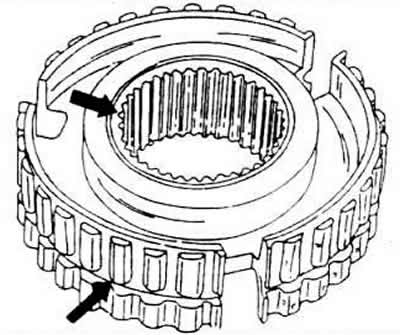
Insert three interlock switches into the switching sleeve and slide the sliding sleeve onto the sleeve. When installing new parts (bushing and sliding sleeve are always replaced together) the switching sleeve must be provided with a groove on the front side (top arrow) or a groove along the outer perimeter (outer arrow). Otherwise, you have ordered the part incorrectly.

When mounting the synchronizer springs, consider fig. and install the springs as shown, i.e. move the end of the spring on the opposite side by 120°with respect to the other spring. Note that the bevel of the inner ring gear of the hub must be found towards the third gear. On the other side of the hub, on its outer edge, there is a groove that must face towards the fourth gear.
Slide the third gear together with the needle roller bearing onto the shaft (well lubricated with oil) and press the synchronizer, but at the same time turn the synchronizer ring so that the groove lies in line with the blocking switches. Check again the chamfer on the inside of the bushing (it should be facing third gear).
To mount the synchronizer, use a new snap ring, but make sure that the ring fits perfectly into the groove.
Fit the 4th gear together with the needle roller bearing (well lubricated with oil) and press firmly.
Press the ball bearing together with the compensation washer into the gearbox housing. Follow that. so that the closed side of the bearing faces the fourth gear.
Output shaft
The fifth gear of the secondary shaft is located above the gearbox housing. The crankcase contains a needle roller bearing.
Both input shaft tapered roller bearings will break if pressed out. In this case, replace the bearing cap together with the bearing at one end and the outer working ring housed in the bearing housing at the other end. If this work is carried out, the adjustment must be carried out again.
A number of changes have been made to the gearbox designed for this engine, affecting the configuration of the shaft. The changes concern (we list just a few of them) an increase in the diameter of the teeth of the fixed gear of the fourth gear, the appearance of an additional groove on the gear of the third gear and the already mentioned parts intended for fastening the gear of the fourth gear; an increase in the snap rings. When ordering new parts, it is best to always state the transmission number.
If old parts are reused, lubricate the bearing cages with oil and insert the shaft into the bearing housing. Finally, mount the bearing cover. Rotate the cover correctly as the reverse gear stopper must be on the same side as the reverse shaft.
If new bearings are mounted, they must be heated in an oil bath to a temperature of 100°C and the corresponding ends must be pressed onto the shaft. In this case, the inner ring of the lower bearing must be well supported.
Check the synchronizing rings and mount the synchronizer parts. The degree of wear is 0.5 mm. The gap between newly installed parts is 1.1-1.7 mm.
Slide thrust washer 12 so that the shoulder faces the bearing cap.
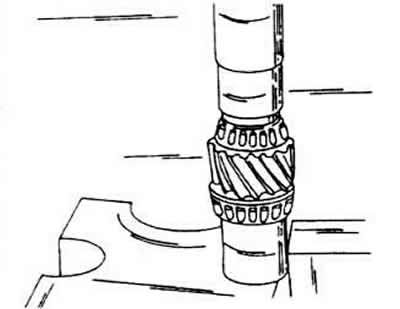

Heat the synchronizing sleeve of the first - second gear 8 together with the synchronizing ring 9 to 120°C and press it onto the shaft using a piece of pipe. The teeth of the synchronizing sleeve must face the first gear.
Mount the reverse shaft together with the reverse gear. If necessary, the shaft must be driven in.
Press or drive the needle roller bearing inner race 7 for the second gear onto the shaft and slide it all the way up to the needle roller bearing gear.
Slide the second gear 6 onto the needle roller bearing.
Heat the third gear 5 and press it from the end of the shaft so that its shoulder faces the second gear. The snap ring should snap into the groove.
Measure the axial clearance of the third gear. Usually take a snap ring and insert it into the groove (gear is tight). Since there is no suitable selection of circlips available, a measurement is made with a thickness gauge. Using the obtained size, you can order a snap ring. In order to correct the gap, circlips are available in various thicknesses (2.5-3.0mm). Remember that the circlips designed for the gearbox of this engine have a larger diameter (with the same thickness).
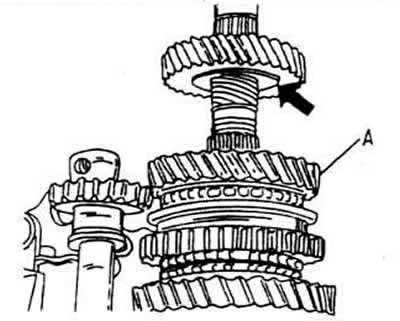
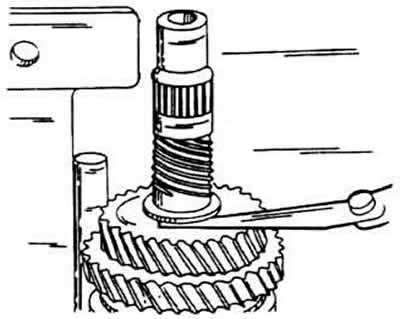
Mount the fourth gear 3 - shoulder up - and place a new circlip 2. Press it well into the groove. As already mentioned, the 2L engine gearbox uses a second circlip.
Press the deep groove bearing onto the shaft. The wide shoulder of the bearing inner ring must face the press punch.
Mount the preloader (it can only be installed in one position), and then tighten it all the way down.
Before installing the fork block, insert the spring into the hole in the clutch housing. It is located in front of the gears.
Re-insert the switching forks in the reverse order to dismantling.
The reverse shaft should be aligned according to the instructions. To do this, screw the screw into the threaded hole of the reverse shaft and insert the shaft into its pilot hole so that the line mentally drawn through the screw head passes in the middle between both screw holes in the gearbox housing. In this position, drive the shaft against the stop towards the bearing cover.
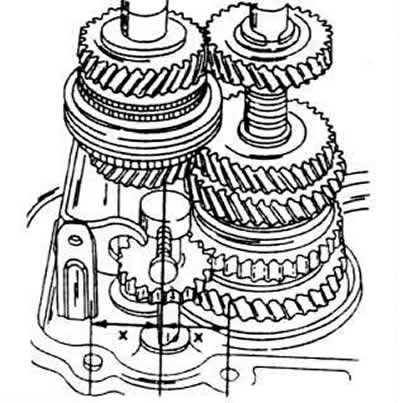
Mount the gearbox housing as described below.
Assembly and installation of the differential
Heat the new differential bearings to 100°C and press them onto the trunnions. Suitable pipe sections can be used for this. A piece of pipe must also be placed under the differential box to reinforce it on the other side.
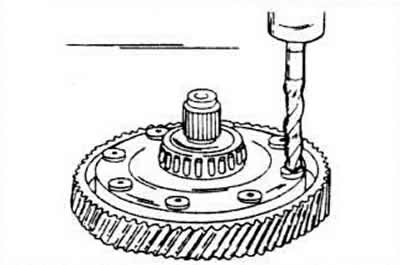
In case of replacing a large drive gear, it is necessary to drill out the rivets (12 mm). This won't cause too much trouble since each rivet is punched in the center. After that knock out the rivets.
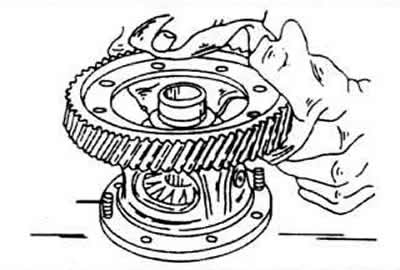
To mount the large drive gear, heat to 100 CC and press onto the differential box. On opposite sides, two guide screws must be screwed into the box (A), to guide the gear during pressing. Use a thick cloth when installing flat bevel gear. Order new special screws, lock washers and nuts (N 171 498 088 A, repair kit) and nuts up to a torque of 70 Nm.
If only the pinions have been dismantled, and the flat bevel gear has not been unscrewed, both sawn-off rivets must be replaced with the two screws mentioned above.
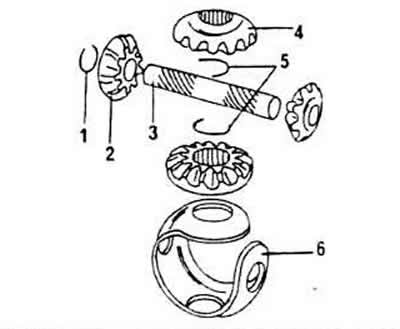
1 - snap rings on the original shaft no snap rings)
2 - satellite bevel gears
3 - differential gear axle
4 - side gear
5 - internal snap rings
6 - ball bearing cage
Install the bevel gears together with the ball bearing cage. Drive in the differential axle carefully, being careful not to damage the cage holes.
Insert the side gears into the hole to turn the bevel gears into position.
Enter the input shafts and then determine the thickness of the inner circlips as follows.
Press the flange mounted on the side of the input shaft to the differential axle and move the gear against the wall of the differential box.
Insert the circlip, checking. so that it is not stuck anywhere. Otherwise, use a smaller circlip.
Position the circlip on the other side in the same way and insert it.
The differential is mounted in the reverse order of dismantling. The differential must be inserted before mounting both flanged shafts.
Assembling the gearbox housing
The gearbox housing is assembled in the reverse order of disassembly, but the following aspects must be taken into account.
Make sure the reverse shaft is in the correct position.
Screw two M8 studs into the bearing shield, which will serve as guides for the gearbox.
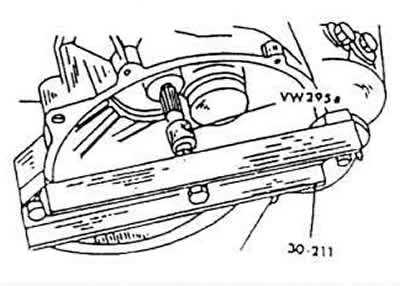
Screw the bridge of the gearbox, and put on the crankcase. Tap the crankcase with a rubber mallet. Don't forget to insert a wear washer for the bearing.
Screw in the reverse shaft screw. Tighten (20 Nm) you need it with a special end kit, since it is a cap screw «Torx».
Screw in the reverse light switch.
Tighten the deep groove bearing clamp plate to 15 Nm.
Screws inserted between both halves of the crankcase, tighten to a torque of 25 Nm. These two screws are shorter in length and fit under the shift shaft screw.
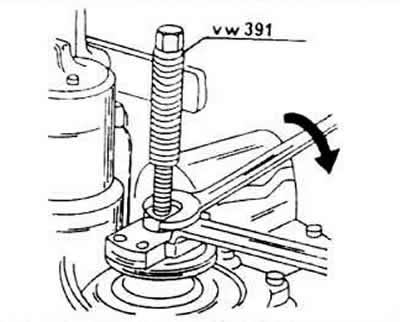
When installing the drive side flange, position the tool as shown in fig. Put the retaining ring on the shaft and drive the ring with a piece of pipe of a suitable diameter until it enters the groove. Hit the cap.
Heat the fifth gear to 100°C and drive it onto the shaft with the groove up. In this, install the snap ring. In this gearbox, you need to pay attention again to the special retaining ring.
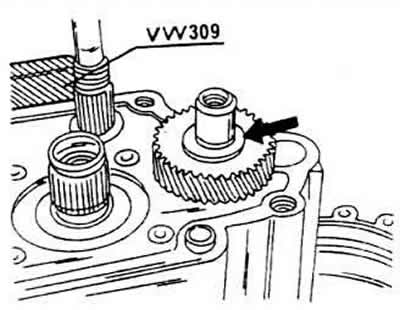
Fit the synchronizing shift sleeve together with the gear and selector fork and mount the new stop plate.
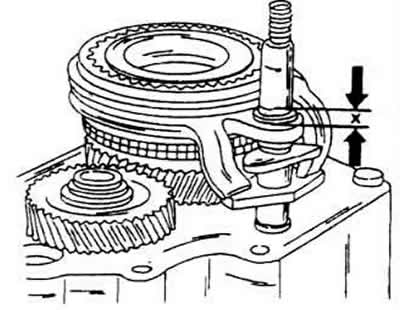
Screw the switch tube clockwise into the switch fork and unscrew it again. until it protrudes 5 mm. Measure the size in the place indicated in Fig. When removing the socket wrench, do not pull out the shift bar, otherwise the shift from the inside will fail and the gearbox will have to be disassembled again. If necessary, to hold the shift lever in its position while the key is removed, insert a screwdriver from the side through the slot.
Lubricate the new switch bushing screw with thread protector D6 and tighten it to a torque of 150 Nm using an M12 Allen key (wrench with internal polyhedron, designed for 12 teeth). Insert reverse gear and fifth gear to block the shaft.
Switch the forks to the idle position and install the shift shaft. To do this, align the gearbox horizontally and secure the tin case with a piece of electrode wire so that it cannot turn.
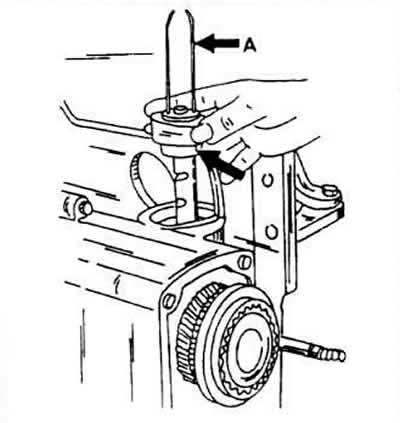
Mount the spring and cap and tighten the cap with a socket wrench to a torque of 50 Nm.
Lubricate the stop screw of the selector shaft with AMV 188 200 03 and insert it. Tighten the screw to a torque of 40 Nm.
Now adjust the fifth gear fork as follows. The adjustment must be carried out carefully to prevent the transmission from jumping out in the future.
Check the size again (X). It should be 5 mm.
Mount the lever on the shift shaft and engage fifth gear by fully pulling the shaft out and turning it to the left.
Using the shift fork, slightly raise the sliding sleeve of the synchronizer to eliminate all gaps in the parts.
Check the quality of engagement of the sliding clutch with the gear teeth. The overlap should be 1 mm. Otherwise, move the switching tube.
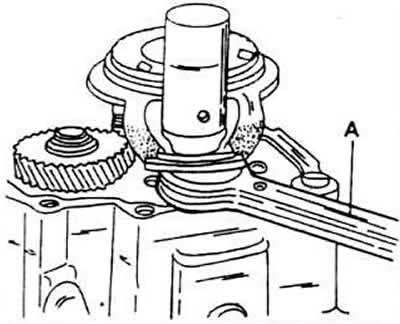
Mount the lock plate. Tool 3097 is required for this. Place two fork spanners under the fork (spanners 19 and 24 mm).
Insert a new cover seal. Push the clutch release lever onto the input shaft. Before doing this, the screwed support bridge must be relieved of tension.
Install the release bearing on the clutch release lever.
Carry out all other work in sequence. reverse disassembly.
Visitor comments