If necessary, remove the wiring harness wrap with a jackknife.
Lay the yellow repair wire next to the damaged wire and use a wire stripper to cut the repair wire to the required length.
Cut out the damaged piece of wire.
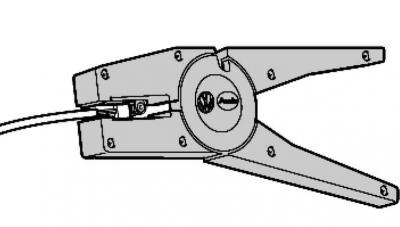
Pic. 7.132. Wire stripping
Strip 6-7 mm of insulation from the ends of the wire using a wire stripper (pic. 7.132).
Push the crimp sleeve on one side onto the end of the wire in the car, on the other side onto the end of the repair wire.
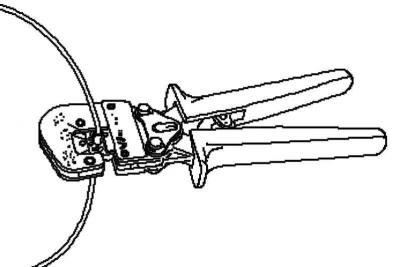
Pic. 7.133. Crimping of a crimp sleeve
Crimp the crimping sleeve with crimping pliers with both ends of the wires (pic. 7.133).
Repeat the same on the other end of the repair wire.
Note: Be sure to use the correct ferrule for the used ferrule.
Note: The wire insulation must not be crimped.
After crimping, the crimp sleeve must be seated to prevent moisture from entering it.
Install the nozzle on an industrial hair dryer, 220 V / 50 Hz.
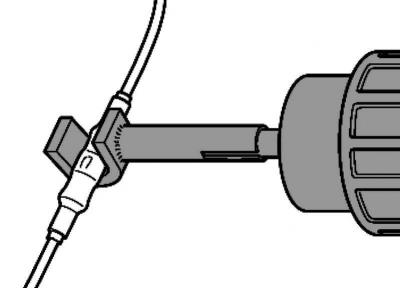
Pic. 7.134. Heating up the crimp sleeve
Heat the crimp sleeve with a hair dryer in a longitudinal direction from the middle to the edges until it shrinks completely and glue comes out at the ends (pic. 7.134).
Caution: When shrinking crimp connections, be careful not to damage other wires, plastic parts or insulation with the hot air gun nozzle.
Please follow the instruction manual for your hair dryer.
Note: If several wires need to be repaired, a certain distance between the crimp sleeves must be observed. so that the wire harness does not turn out to be too thick in the girth after repair, install the crimp sleeves with some offset relative to each other.
Note: If the originally repaired area was wrapped with electrical tape, then after repair it should be wrapped with yellow electrical tape.
Note: The repaired wiring harness should then be secured with a wire tie, if necessary, to avoid extraneous sounds when driving.
Visitor comments