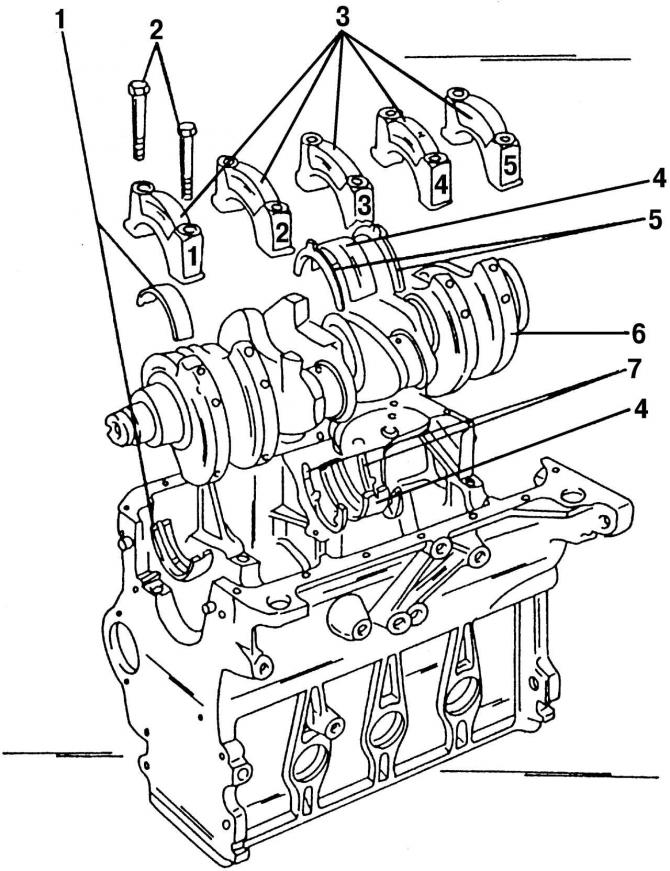
Pic. 440. Crankshaft bearings: 1 - bearing shells No. 1, 2, 4 and 5. The shells with grooves for lubrication are located in the cylinder block, the shells without lubrication grooves are located in the bearing caps; 2 - cover bolts, 65 Nm + 90 Nm; 3 - covers of main bearings, cover No. 1 is located on the side of the pulleys, cover No. 3 has recesses for adjusting washers; 4 - bearing shells No. 3. A liner with a lubrication groove is located in the cylinder block, a liner without lubrication grooves is located in the bearing cap; 5 - adjusting washers for bearing No. 3; 6 - crankshaft; 7 - adjusting washers bearing No. 3, located in the cylinder block
Before removing the crankshaft, which can only be done on a dismantled engine, measure the axial clearance to know when assembling whether it is necessary to change the shims on the middle main bearing (pic. 440).
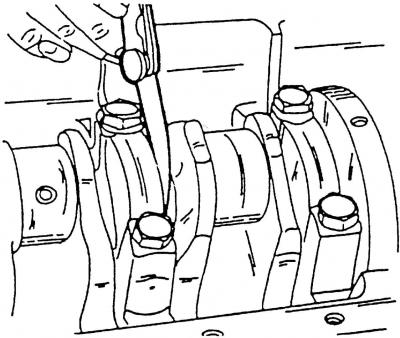
Pic. 441. Measuring the axial clearance of the crankshaft with a feeler gauge
Insert a feeler gauge on the middle bearing (number 3) between the crankshaft web and the inserted shim, as shown in fig. 441 and check the axial clearance, which should be between 0.07 and 0.17 mm. The largest gap should not exceed 0.37 mm.
Pay attention to the fact that the axial clearance is completely selected, for which rest the lever (it is best to use a wooden handle of any tool to avoid damage) into the cheek of the crankshaft and use it to press the shaft to the side. By inserting feeler gauges of various thicknesses, set the exact gap.
Axial clearance can be measured using an indicator, which should be attached to the end side of the cylinder block, and install the measuring finger on the end of the crankshaft. After that, press the crankshaft in the direction of the indicator. Set the indicator to zero and press the shaft in the opposite direction. Look at the gap on the indicator.
Visitor comments