Lubricate the cylinder bores liberally.
Lay out all connecting rods according to cylinder numbers. The cast lugs on the connecting rod and connecting rod cap must point towards the intermediate shaft.
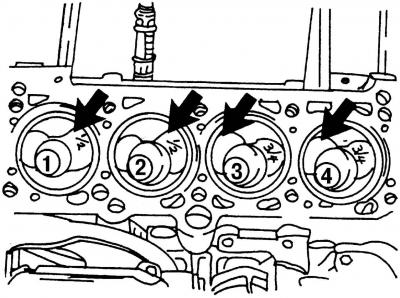
Pic. 422. View of the top of the engine. The arrows show the large inlet valve recesses, which are positioned differently on pistons #1 and 2, #3 and 4
Lay out all pistons in the order in which they were installed (pic. 422).
Distribute the piston ring locks over the cylinder surface so that they are at an angle of 120°relative to each other.
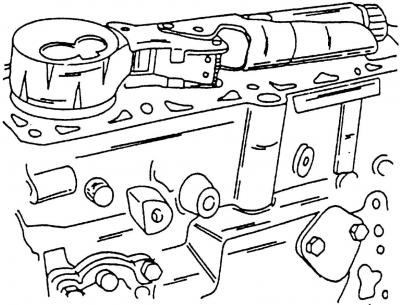
Pic. 431. The use of a clamping band when installing pistons
Put a mandrel for installing the piston with rings in the cylinder on the area where the piston rings are located (pic. 431) and press the piston rings into the piston grooves. Check that the piston rings are fully engaged in their grooves. If you do not have a special mandrel, then you can use a thin metal strip that you wrap around the piston rings and squeeze so that the rings fit into the grooves on the piston.
Turn the crankshaft so that the two connecting rod journals of the crankshaft are at BDC.
Insert the connecting rod from above into the cylinder bore. To do this, lay the engine on its side so that the connecting rod can be directed to the main journal without scratching the cylinder surface and the connecting rod journal. The connecting rod bearing shell should already be in the connecting rod with the protrusion in the recess.
Insert the pistons in such a way that the rings in turn enter the cylinder bores and the connecting rod heel sits on the crankshaft crankpin.
Insert the second bearing shell into the bearing cap so that the bearing shell is seated in the groove of the bearing cap, and lubricate the shell surfaces well. Press the connecting rod cap against the connecting rod and lightly tap it.
Attention! Make sure both molded lugs are together.
Lubricate the connecting rod bolts and connecting rod threads with oil.
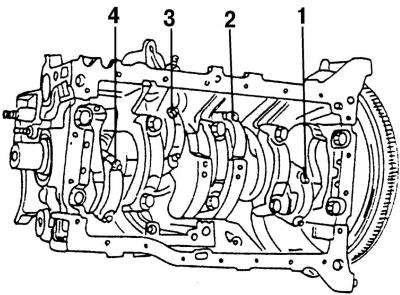
Pic. 432. Tighten the bolts shown to 30 Nm + 90°
The connecting rod bearing bolts are tightened according to a certain scheme. As already mentioned, always replace the bolts with new ones. Alternately tighten the connecting rod bearing bolts (pic. 432) torque of 30 Nm and then turn them from their end position by another 90° (a quarter turn), without using a torque wrench.
Attention! When measuring the axial clearance of the connecting rod bearings, use the old connecting rod bearing bolts, since when using new bolts for this purpose, they can no longer be tightened a second time.
After installing the connecting rod, rotate the crankshaft several times to immediately make sure that it rotates easily, without jamming.
Check the markings on all connecting rods again to make sure the pistons are pointing in the correct direction. Also make sure that the recesses for the oil jets are on the correct side.
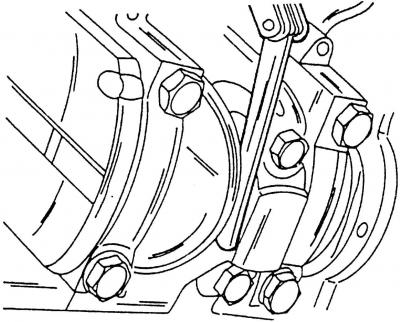
Pic. 433. Measuring the gap between the side planes of the connecting rod and the surface of the crankshaft
Using a feeler gauge, measure the clearance between the side surfaces of the connecting rod and the surface of the crankshaft (pic. 433) - the axial clearance of the connecting rod bearings should not exceed 0.37 mm.
Visitor comments