Caution: When carrying out installation work, especially in the engine compartment due to its dense layout, the following rules must be observed. Pipelines of all kinds (fuel, hydraulic, absorber, coolant, coolant, brake fluid, vacuum) and electrical wires must be laid as they were originally laid. To avoid damage to hoses, pipes or wires, sufficient space must be provided when working on all moving or hot parts. Insert new centering sleeves into the cylinder block (for the correct alignment of the engine and gearbox). Position intermediate plate on dowel sleeves of engine flange -arrows-.
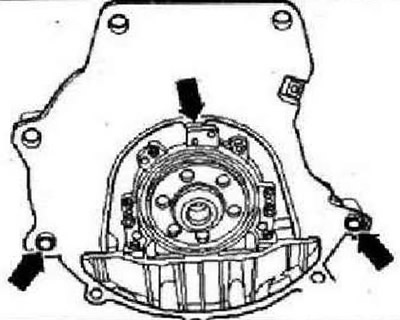
With manual transmission
Apply a thin coat of grease -G OO0100- to splines of input shaft.
With DSC
Replace needle bearing in crankshaft. Adjust selector cable after installation.
All
When installing the power unit, make sure that it does not catch on the subframe or radiator. Electrical connection and wiring. Connect tester -VAS 5051B-. Interrogate the fault memory and delete from it all errors that may have occurred during the installation of the engine. Do a test drive. After that, repeat the diagnostics of the vehicle systems and, if necessary, eliminate the errors that have arisen.
Instruction: After clearing the fault memory, create a readiness code.
Tightening torques
M6 | 10 Nm |
M7 | 15 Nm |
M8 | 25 Nm |
M10 | 40 Nm |
M12 | 60 Nm |
Implement support
Note: The assembly support bolts are malleable bolts and must be replaced.
Engine support
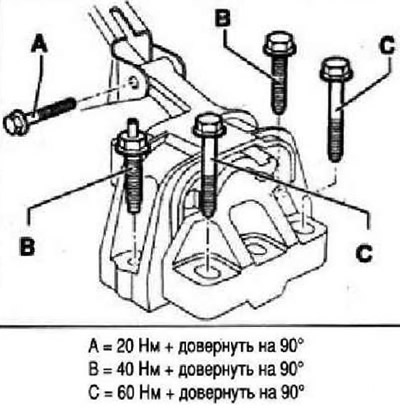
Gearbox support
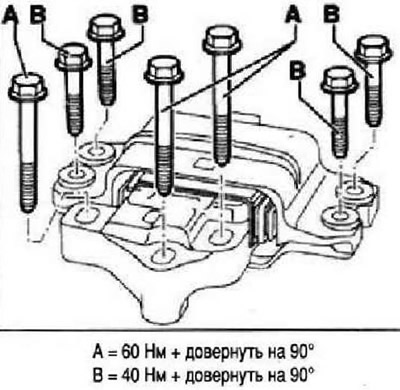
Rocking support
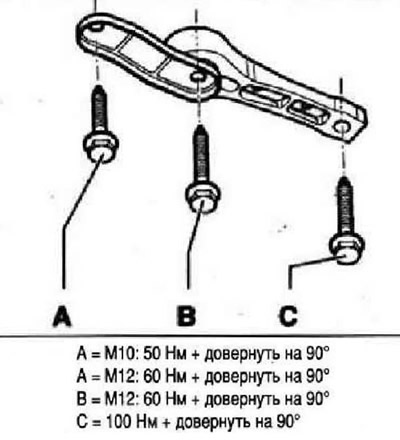
Checking the adjustment of the implement support
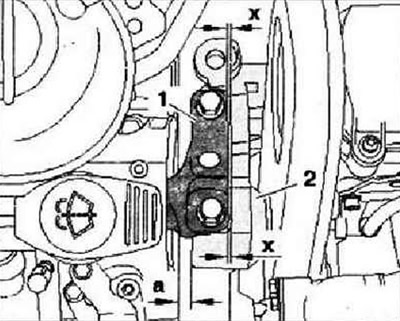
The distance -a- between the engine support and the right side member must be at least 10 mm. The cast edge in the engine support -2- must be parallel to the bracket -1-. If these conditions are not met, the unit support must be adjusted.
Visitor comments