Caution: For any assembly work, in particular in the engine compartment due to the tight layout, the following must be observed. Lines of all kinds (e.g. fuel, hydraulic, activated charcoal absorber, cooling systems, refrigerant circuits, lines and hoses of the brake system, vacuum), as well as electrical wires must be laid as they were originally laid. To avoid damage, ensure sufficient clearance to all moving and hot parts.
Check the clutch release bearing for wear, replace if necessary. Lightly lubricate the release bearing, bearing guide sleeve and input shaft teeth with G 000 100 grease. Hang the intermediate plate on the flange and push it onto the fitted bushings -arrows-.
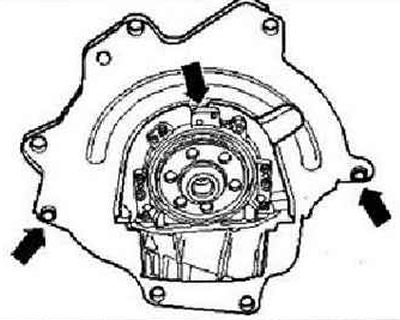
Align the engine mount as follows. The distance -a- between the engine support and the right side member must be at least 10 mm. The cast edge in the engine support -2- must be parallel to the bracket -1-.
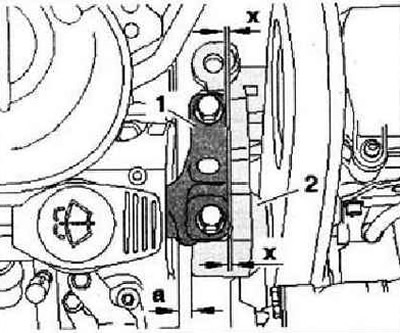
On gearbox side, make sure that bracket 1- is parallel with gearbox console -2-.
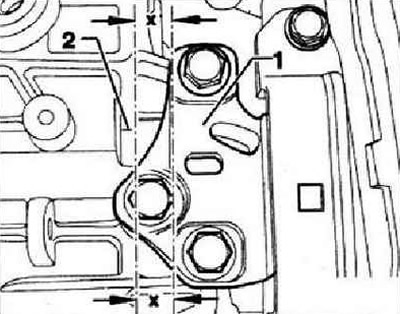
Install gearbox bracket for bevel box. Install the exhaust pipe.
Instructions: First tighten the fixing nuts by hand.
Position exhaust pipe support and tighten securing bolts -1- and -2- to 25 Nm. Install the subframe.
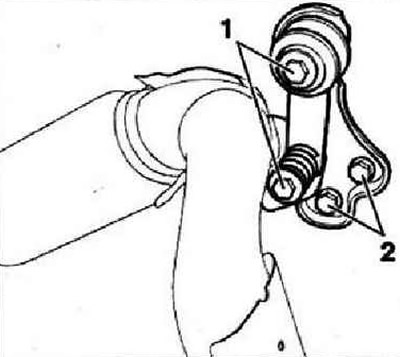
Install driveshaft. Install drive shafts. Install the gearshift drive. Connect hose -1- for hydraulic clutch slave cylinder. Install the power unit lower support. Install the air conditioner compressor. Install poly V-belt. Electrical connections and wiring. Fill with coolant. Install the air filter. Install the battery and battery holder. Connect the battery. Press engine cover at points -1- in -direction of arrow- downwards until it snaps into place at these points. Push vacuum line onto connector -arrow-. Connect tester -VAS 5051 B-. Erase previous readings and adapt control flap control unit and throttle flap control unit. Carry out system diagnostics. Complete the diagnosis of the vehicle's systems so that errors that may have been registered during installation are automatically cleared from the fault memory. Do a test drive. After that, repeat the diagnostics of the vehicle systems and, if necessary, eliminate the errors that have arisen.
Tightening torques
M6 | 10 Nm |
M8 | 20 Nm |
M10 | 45 Nm |
M12 | 60 Nm |
Power unit suspension - tightening torques
Note: The assembly support bolts are malleable bolts and must be replaced.
Power unit suspension, engine
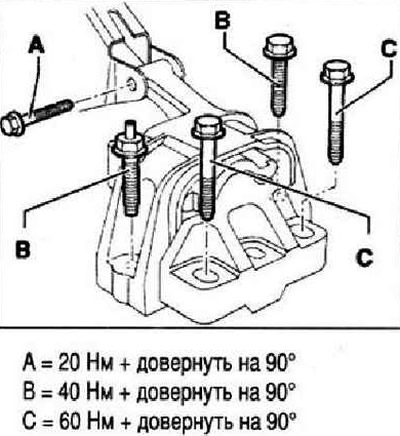
Suspension of the power unit, gearbox
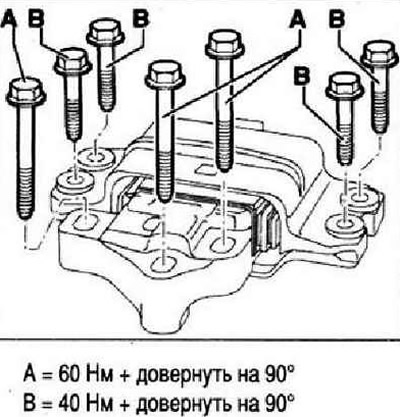
Lower support of the power unit
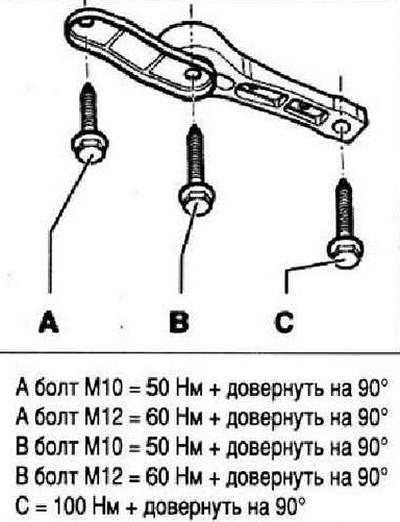
Visitor comments