Removing
Remove crankshaft.
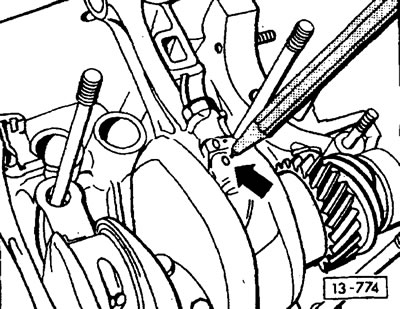
Mark appropriate connecting rods and bearing shells
Loosen the connecting rod nuts and remove the connecting rod caps, connecting rod rods and bearing shells. Mark bearing shells. It is recommended to fold all removed parts in the installation order.
Examination
Inspect the connecting rods for external damage.
The connecting rod cap bolts must not be crushed. If bolts are damaged, replace the entire connecting rod.
Connecting rods must be replaced as a set.
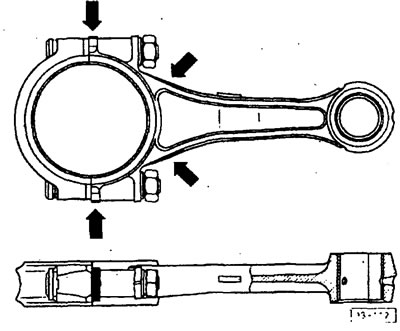
When replacing connecting rods, their weight must be checked, since the difference in weight of individual connecting rods must not exceed? gr. Weigh connecting rods without bearing shells.
If necessary, modify the connecting rods in the places indicated in the figure. In this case, a weight reduction of 8 g can be achieved.
Check the connecting rod head bushing. With a new bushing, an unheated piston plate should enter when lightly pressed with a finger.
If necessary, balance the cranks (service station work).
Installation
Rinse all parts in gasoline and lubricate with engine oil.
Depending on the design, if required, replace the 6 connecting rod caps. There are 2 types of bolts installed:
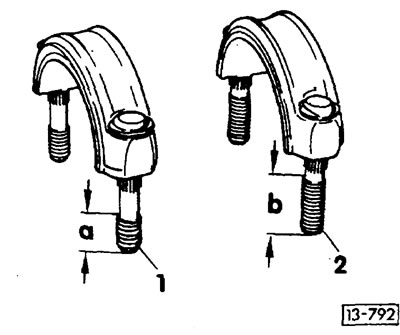
1 - a rigid bolt, the length of the threaded part a is about 13 mm, does not change.
2 - tensile bolt, length of the threaded part b = about 30 mm, must be replaced, since the tensile bolt is released with each tightening. Observe different tightening methods.
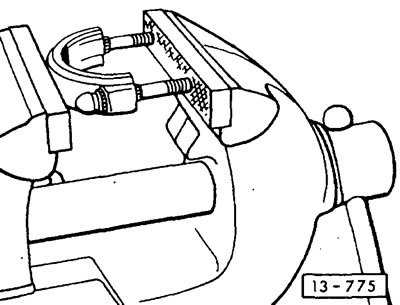
To remove the connecting rod cap bolts, it is advisable to clamp the cap in a vise, as shown in the figure. Using a suitable press, press new bolts into the connecting rod caps.
Insert bearing shells and connecting rods in accordance with the markings made. Details must be installed in their original places.
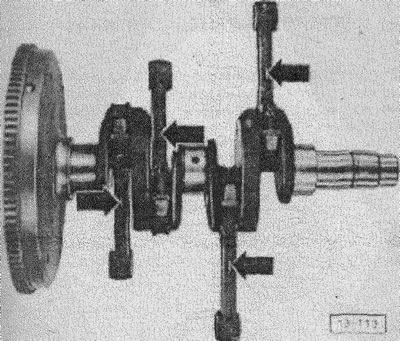
When installing, mark on connecting rod must point upwards -arrows-.
Unfasten new nuts. Remove the protective grease from the nuts first and lubricate them with engine oil.
Tighten the three rigid bolts of the connecting rod caps with the nuts to a torque of 45 Nm.
With tensile bolts (see -2- in figure 13-792) nuts are tightened in 2 passes. This requires a torque wrench.
1st pass: tighten the nuts with a torque wrench to a torque of 30 Nm.
2nd pass: tighten the nuts with a hard wrench by 180° (1/2 turn). For a better reading of the angle of rotation, pre-mark the engine with chalk. There are also special protractors for turning fasteners to certain angles, for example, from Hazet.
After assembly, the connecting rods should tip down under their own weight.

Minor misalignments that occur when tightening the bolts between the bearing halves can be corrected by light hammer blows on both sides of the connecting rod.
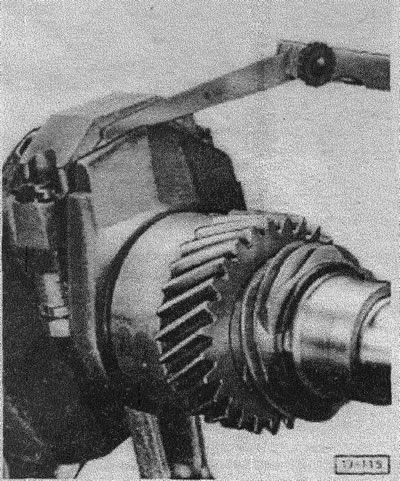
Check the end play of the connecting rod with a feeler gauge. The wear limit is max. 0.7 mm.
Visitor comments