Attention! A diesel engine requires a compression gauge with a large measurement scale.
The pressure difference between the individual cylinders must not exceed 3.0 bar (diesel engine 5.0 bar). If one or more cylinders have a pressure difference of more than 3.0 bar (diesel engine 5.0 bar), then this indicates a defective valve, wear of the piston rings or cylinder walls. When the wear limit is reached, the engine must be rebuilt or replaced.
engine's type | Compression pressure, bar | |
New | wear limit | |
Gas engine | 9 – 12 | 7,0 |
diesel engine | 34,0 | 26,0 |
Gas engine
1. When checking compression, the engine must be at operating temperature. Oil temperature not less than 30°С.
2. Switch off the ignition.
3. Disconnect plug from Hall sender at ignition distributor.
4. Remove fuse #15 from fuse box.
5. Disconnect all spark plugs. Special pliers are available for this, eg HAZET 1849. They only grip the plug by the metal sleeve.
6. Blow out dirt from the spark plug recesses in the cylinder head with compressed air and remove all spark plugs with a suitable spark plug wrench.
7. Rotate the engine several times with the starter to remove combustion products.
Attention! Transmission in neutral position, handbrake applied.
8. Fasten or wrap, according to the instructions for use, the compression gauge in the hole of the cylinder for the spark plug.
9. Squeeze out the gas pedal to the end and during the entire test hold it in this position. This requires an assistant.
10. Crank the engine about 8 revolutions until the pressure gauge shows constant pressure.
11. Check all cylinders in sequence and compare the readings with the required values.
12. Replace spark plugs and connect high voltage wires.
13. Connect the plug to the Hall sensor.
14. Install fuse #15.
Diesel engine
Compression measurement
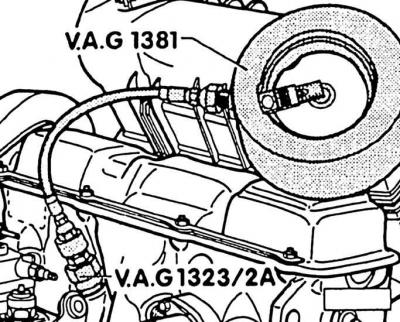
Compressometer VW-1381
Adapter VW1323/2A
Heat insulator
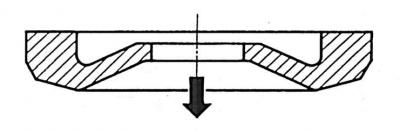
1. Warm up the engine in motion, to a coolant temperature of 80°C.
2. Disconnect the electrical wire from the injection pump fuel switch, insulate and set aside.
3. Clean the injection lines with a cold cleaner and remove without changing their bent shape.
4. Remove nozzles (see subsection 2.17.7.5).
5. Screw in the compression gauge instead of the injector, while installing the old heat insulator between the compression gauge and the cylinder head.
Attention! The given pressure data is only valid when measured with a VW-1381 compression tester with VW1323/2A adapter. Other instruments can only measure the difference in pressure between the individual cylinders (see fig. Compression measurement).
6. Crank the engine about 8 revolutions until the meter reading stabilizes.
7. Screw nozzles on and tighten to 70 Nm.
Attention! Heat insulators between cylinder head and injectors must always be replaced. The recess must be installed upwards (see fig. heat insulator).
8. Tighten injection lines to 25 Nm.
9. Connect the wire to the fuel switch.
Visitor comments