Головка цилиндров
При наличии коробления, превышающего допускаемые величины, поверхность головки следует подвергнуть фрезерованию или шабрению. При фрезеровании необходимо помнить, что уменьшать объем камеры сжатия допускается не более чем на 1,5 см3. Контроль фрезерования или шабрения должен осуществляться набором щупов на контрольной плите или при помощи лекальной линейки (рис. 8.12).
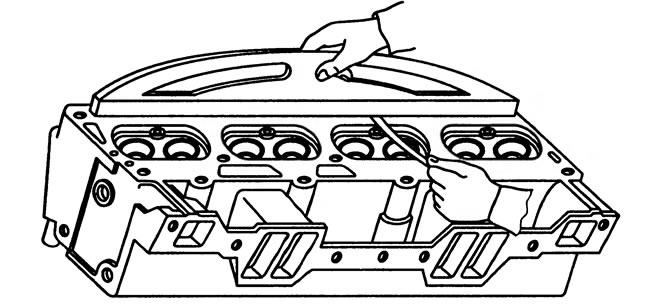
Рис. 8.12. Определение отклонения от плоскостности головки цилиндров при помощи лекальной линейки
Трещины в рубашке охлаждения, прогары по перемычкам между камерами сгорания, разрушения под действием коррозии, износ поверхности в зоне отверстий для свечей зажигания ликвидируется заваркой проволокой АК-5 (ГОСТ 7871—75) в среде аргона с последующей зачисткой следов сварки в камере сгорания и восстановлением размеров.
Поврежденные резьбовые внутренние поверхности отверстий восстанавливают спиральными резьбовыми вставками. При этом фаски в отверстиях для вставок и выступание наружу первого витка вставки не допускаются. Испытание головки цилиндров на герметичность следует проводить водой или эмульсией под давлением 0,3 МПа.
Клапаны
Клапаны изготовлены из жаростойкой стали, стержни клапанов хромируются. Восстановление герметичности клапанов осуществляется притиркой рабочих фасок клапанов к их седлам. При наличии на рабочей фаске клапана раковин или рисок, которые нельзя ликвидировать притиркой, фаску подвергают шлифованию с последующей притиркой к седлу.
Вращение клапана в процессе ручной притирки проводится с помощью специальной дрели (рис. 8.13), поворачивающей клапан поочередно в обе стороны. Захват головки клапана осуществляется резиновой присоской. Во время притирки под клапан рекомендуется устанавливать пружину с небольшой упругостью. Для ускорения притирки используют притирочную пасту или мелкий наждачный порошок, смешанный с маслом, которое применяется для смазывания двигателя.
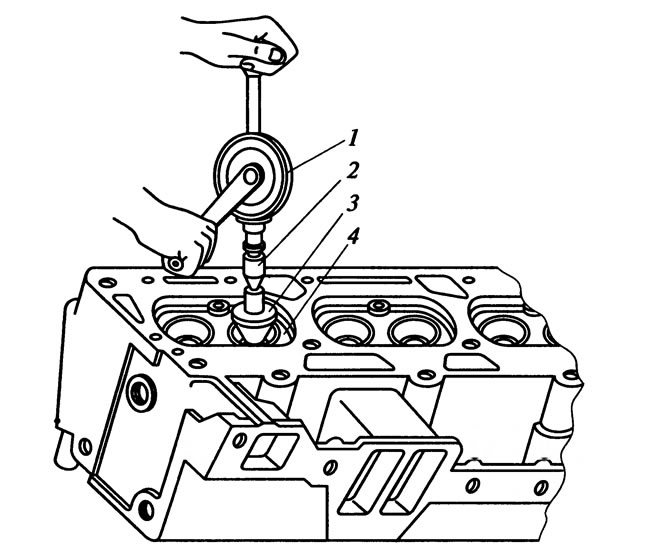
Рис. 8.13. Притирка клапанов с помощью дрели: 1 - дрель; 2 - присоска; 3 - клапан; 4 - седло
Стержень клапана должен быть прямолинейным. Проверка отклонения от прямолинейности проводится с помощью индикатора на призмах (рис. 8.14, я). Допуск на непрямолинейность стержня клапана не должен превышать 0,015 мм на 100 мм длины. Биение рабочей поверхности фаски клапана относительно оси стержня проверяют на специальном приспособлении (рис. 8.14, б). Величина биения рабочей поверхности фаски клапана не должна превышать допустимого размера.
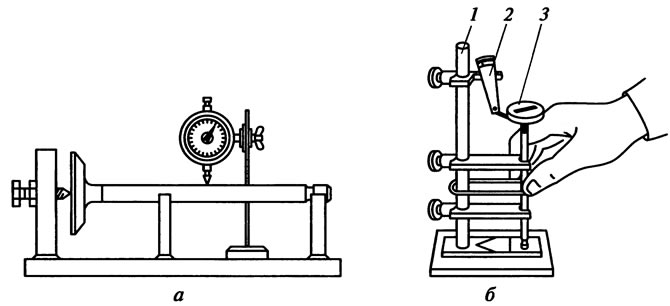
Рис. 8.14. Проверка клапана: а - проверка отклонения от прямолинейности стержня; б - проверка торцового биения рабочей поверхности фаски; 1 - стойка приспособления; 2 - измерительное устройство; 3 - клапан
При обнаружении выработки (износа), если имеются раковины или риски на рабочей фаске, клапан подвергается шлифованию. Рабочие фаски клапанов можно шлифовать на специальном настольном шлифовальном станке мод. 2178 или на круглошлифовальном станке с креплением клапана в цанговом патроне 3 (рис. 8.15). Конструкция станка позволяет устанавливать клапан под требуемым углом к шлифовальному кругу. Фаску впускного клапана шлифуют под углом 30° (относительно горизонтальной оси), а выпускного — под углом 45°. На станке можно также проводить шлифование торца стержня клапана при его износе.
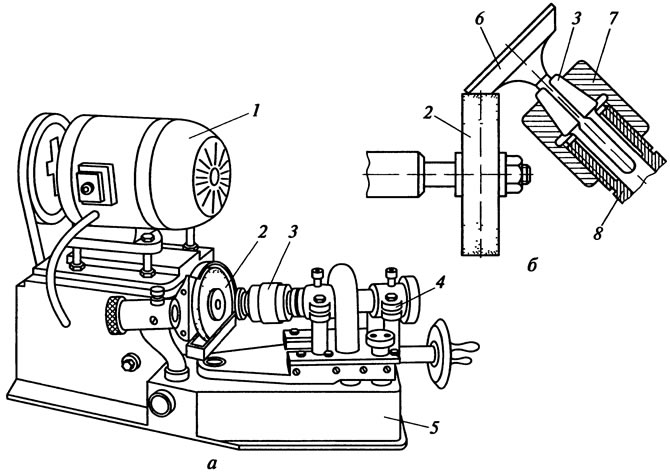
Рис. 8.15. Шлифование фасок клапана на круглошлифовальном станке: а - общий вид; б - схема шлифования; 7 - электродвигатель; 2 - шлифовальный круг; 3 - цанговый патрон; 4 - суппорт; 5 - станина; 6 - клапан; 7 - гайка; 8 - корпус патрона
Испытание клапанов на герметичность можно осуществлять специальным прибором мод. НИИАТ. Для этого прибор плотно устанавливают над притертым клапаном и с помощью груши нагнетают воздух в пространство станка (рис. 8.16). Если при этом избыточное давление воздуха 0,07 МПа не падает в течение 30 с, то клапан притерт хорошо. После притирки и проверки герметичности клапанов головку цилиндров и клапаны следует тщательно промыть и продуть сжатым воздухом.
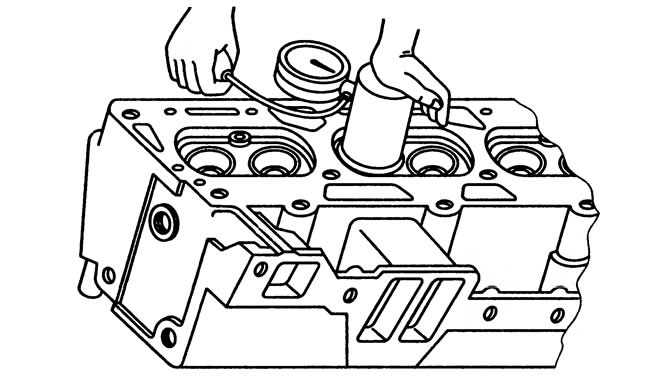
Рис. 8.16. Проверка клапана на герметичность с помощью прибора мод. НИИАТ
Втулки клапанов
Втулки клапанов запрессованы с натягом 0,014...0,065 мм. Втулки ремонтных размеров имеют больший наружный диаметр на 0,25 мм и меньший внутренний на 0,7 мм. Обработка внутренней поверхности втулки до номинального диаметра проводится в сборе с головкой цилиндров. Максимально допустимый износ отверстия втулки клапана должен быть не более 0,05 мм.
При большем диаметре втулку следует заменить. Выпрессовка втулок клапанов проводится с помощью специального съемника (рис. 8.17, а). При запрессовке втулки 9 клапана (рис. 8.17, б) в отверстие головки цилиндров 7 необходимо надеть на втулку стопорное кольцо и запрессовать втулку с помощью оправки 8 до упора стопорного кольца в головку. Для облегчения запрессовки втулок головку цилиндров рекомендуется нагреть до температуры 180°C.
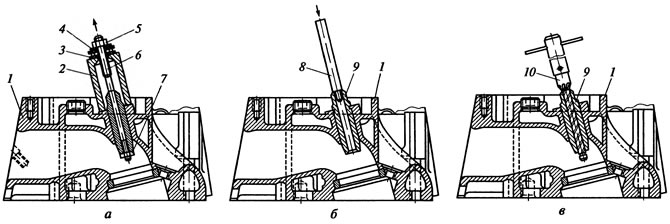
Рис. 8.17. Замена втулок клапанов: а - выпрессовка втулки; б - запрессовка втулки; в - подгонка втулки разверткой; 1 - головка цилиндров; 2 - корпус съемника; 3 - упорный подшипник; 4 - шайба; 5 - гайка; 6 - стержень; 7 - опорная гайка; 8 - оправка; 9 - втулка; 10 - развертка
После запрессовки втулку необходимо подогнать разверткой 10 (рис. 8.17, в) под диаметр устанавливаемого в нее стержня клапана, сохраняя при этом тепловой зазор между втулкой и стержнем. Зазоры во втулках клапанов рекомендуется сохранять в пределах, рекомендованных заводом-изготовителем, так как с их увеличением ухудшается теплоотдача, что отрицательно сказывается на долговечности фаски клапана. Замену втулок клапанов следует проводить до ремонта седел клапанов.
Клапанные пружины
Пружины проверяются методом проверки их длины в свободном и нагруженном состоянии. Размеры нагрузки и длины пружин устанавливаются заводом-изготовителем. Высоту и упругость пружины проверяют на приборе мод. НИИАТ. Нагрузку на пружину определяют по динамометру. После освобождения пружины от груза она не должна иметь остаточной деформации. Пружины, не отвечающие требованиям, заменяются.
Толкатели
Толкатели изготовляются из стали пустотелыми. Для повышения работоспособности сопрягаемой пары толкатель—кулачок на торец толкателя наплавлен специальный чугун. Износ сферической поверхности толкателя не должен превышать 0,1 мм.
Изношенные толкатели должны быть заменены новыми. Завод изготовляет толкатели нескольких размерных групп. Маркировка обычно нанесена на наружной поверхности толкателя. Толкатель, правильно подобранный к направляющему отверстию в блоке, должен плавно опускаться в отверстие под действием собственной массы. При этом толкатель должен быть смазан тонким слоем масла.
Седла клапанов
Седла изготовлены из специального чугуна. Перед запрессовкой седел клапанов головку цилиндров следует нагреть до температуры 180°C. Запрессовка (рис. 8.18) проводится при помощи специальной оправки до упора седла в гнездо. Износ фаски седла приводит к неплотному прилеганию клапана, при этом прорывающиеся газы образуют оксидные пленки и раковины на рабочей поверхности фаски, а иногда и на клапане.
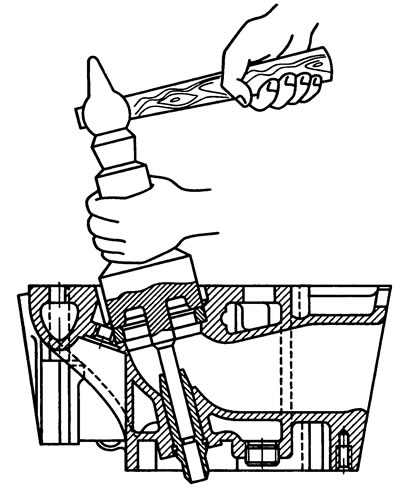
Рис. 8.18. Схема запрессовки седла клапана в головку цилиндров
Небольшое повреждение можно устранить притиркой клапана к седлу, а глубокие риски — шлифованием с последующей притиркой клапана к фаске седла. Для шлифования седел впускных клапанов применяют конусный абразивный инструмент с углом наклона кромки 30° относительно горизонтальной оси, а для шлифования седел выпускных клапанов используют инструмент с углом наклона кромки 45°.
Прежде чем произвести исправление седла клапана, следует проверить состояние втулок клапанов. Если втулки необходимо заменить, то нужно выполнить сначала эту операцию, а затем приступать к шлифованию седел, так как базой для обработки седел являются втулки клапанов. Чистовое шлифование следует проводить абразивным инструментом. Точность обработки седла контролируется с помощью индикатора (рис. 8.19). Допуск радиального биения рабочей поверхности седел клапанов относительно оси отверстий втулок клапанов составляет 0,05 мм.
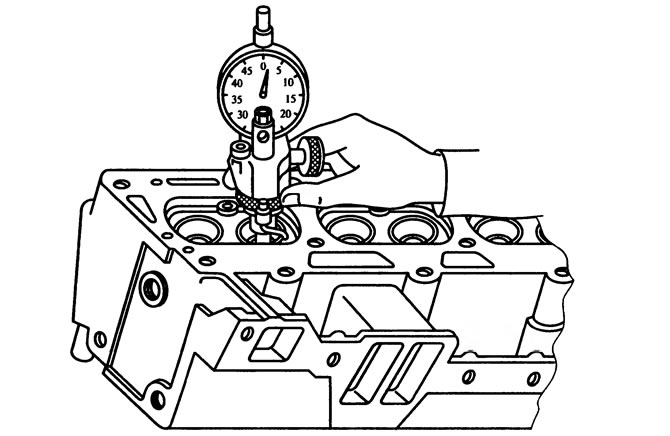
Рис. 8.19. Проверка точности обработки седла клапана
Изношенные седла, которые невозможно исправить шлифованием, выпрессовывают из головки с помощью специального приспособления (рис. 8.20) и заменяют новыми. Затем обрабатывают фаски новых запрессованных седел, добиваясь их соосности с направляющими втулками, и притирают к ним клапаны. После ремонта седел клапанов головку цилиндров надо тщательно промыть и продуть сжатым воздухом.
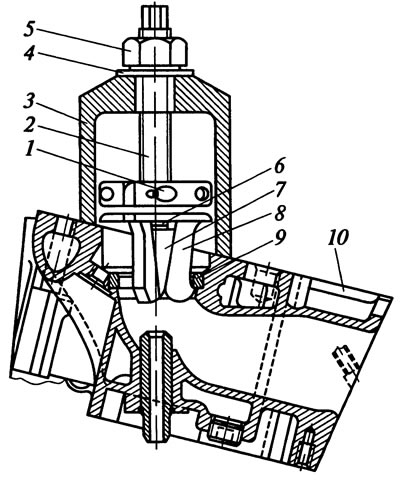
Рис. 8.20. Схема приспособления для выпрессовки вставного седла клапана из головки цилиндров: 1 - специальная гайка с тремя лапками; 2 - винт с разжимным конусом; 3 - корпус приспособления; 4 - шайба; 5 - гайка; 6 - стяжная пружина; 7 - разжимной конус лапок; 8 - лапка приспособления; 9 - вставное седло; 10 - головка цилиндров
Прокладка головки цилиндров
Прокладку головки цилиндров рекомендуется заменять при каждом снятии головки. При установке прокладки на блок важно так установить прокладку, чтобы она встала в соответствии с маркировкой «Верх», а края ее не попадали в камеру сгорания двигателя.
Комментарии посетителей